IRD Continuous Processing
Infrared crystal dryer can be used for PET, PLA, TPU, TPE HIPS, PE, ABS, EVA ,PC, PEEK, PPS, PTFE, PEEK e.g.
Infrared crystal dryer continuous processing
Infrared drying technology offers the ability to dry and crystallize materials in minutes, compared to hours with conventional drying equipment which reduces change over times significantly and reduces energy consumption at almost 45%, Also Infrared drying technology changes in moisture at beginning will dry pellets gently to a uniform degree within minutes, the final moisture can be 150ppm.
The infrared dryer ODE Made can be used for a variety of plastic pellets, such as APET, GPET, CPET, PLA, HIPS, PE, ABS, EVA ,PC, PEEK, PPS, PTFE, PEEK, TPU, TPE e.g.
Infrared crystal dryer Model
Model Number |
IRD-80 |
IRD-200 |
IRD-300 |
IRD-500 |
IRD-1000 |
Output/Capacity |
/ |
200 |
300 |
500 |
800-1000 |
Installation Heating power |
/ |
21 |
36 |
52 |
135 |
Drying time |
Normally 20mins |
||||
Control |
By Siemens Touch Screen PLC system |
||||
Processing |
Dehumidifier and crystallized at a time |
||||
Final moisture |
100-150ppm |
||||
Heating way |
Infrared lamps |
||||
Energy saving |
Up to 45% |
||||
Space saving |
Up to 300% |
||||
Operation |
Faster to start up |
IRD inside structure for reference
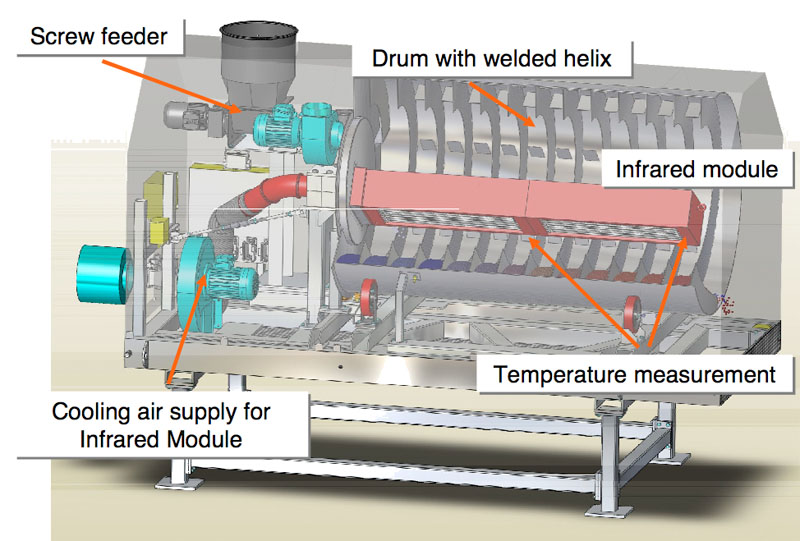
Convey the material to the Infrared dryer drum.
The entranced material flow will go by welded helix channel on the drum surface while the drum rotates. During the processing, the material will be dried evenly by turning over and conveyed out.
Used to provide a heat source to evenly illuminate the material.
Imported from Germany, the temperature information of particles/Scraps in the drum will be fed back to Siemens PLC in time to realize the intelligent regulation of temperature.
Prevent dust from adhering to the wall of the lamp tube, affecting lamp life and heating efficiency; causing temperature difference in the drum, which is conducive to the diffusion of water vapor.
Advantage
No |
Infrared crystal dryer |
Conventional dehumidifier and crystallizer |
Comparison: |
||
1 |
Processing |
|
Dry and crystallizer at one step processing |
Dehumidifying and Crystallizer separated |
|
2 |
Drying time |
|
20mins |
Dehumidifying 4-5hours |
|
3 |
Energy cost |
|
Installation power: 42kw |
Installation power: 156kw |
|
Infrared crystal dryer Energy savings up to 45% |
||
4 |
Space saving |
|
Infrared crystal dryer is up to 300% space saving |
||
5 |
Maintenance |
|
Infrared lamp working life 7000-10000hours. If broken, just pull it out and insert new lamp. And all lamps are controlled by PLC system, no need to adjust the heating temperature |
Molecular sieve have to be examed at regular time. If blocked, you have to changed all Molecular sieve and adjust the dew point and test the dryer again |
|
|
Infrared crystal dryer is much easier for start, operate and maintenance |
Machine photos
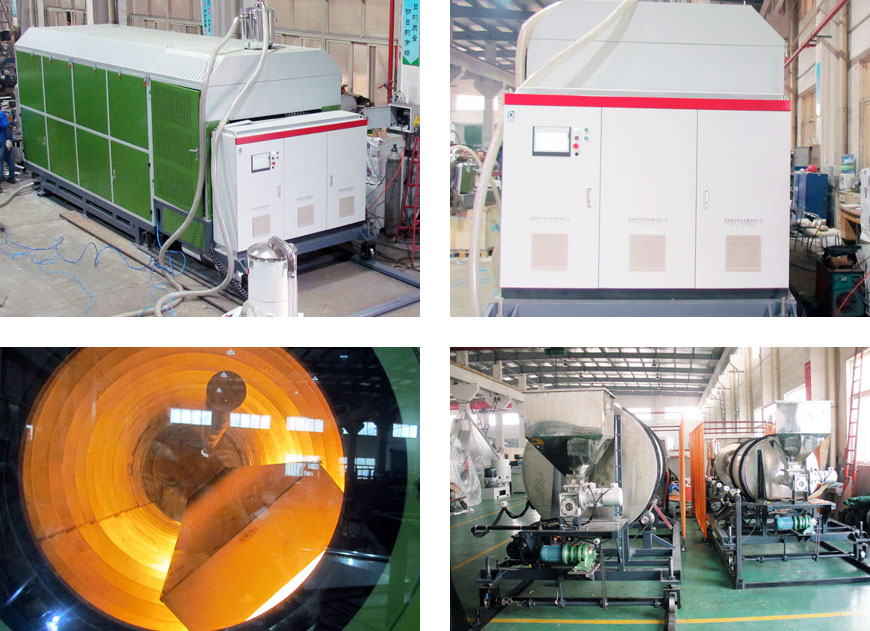
Application examples
Drying and crystallizing of PET to 50PPM
Drying and crystallizing of PLA
Drying of TPU
Drying and heating of PE pellets to remove volatiles
Crystallization of masterbatch in small batches
Drying and crystallizing of PET for pelletizing or sheet extrusion
Drying and crystallizing of PLA for pelletizing or sheet extrusion
Drying and crystallizing of PPS Pellets, amorphous Co-Polyester
Drying, crystallizing and heating of bulk materials
Processing sample
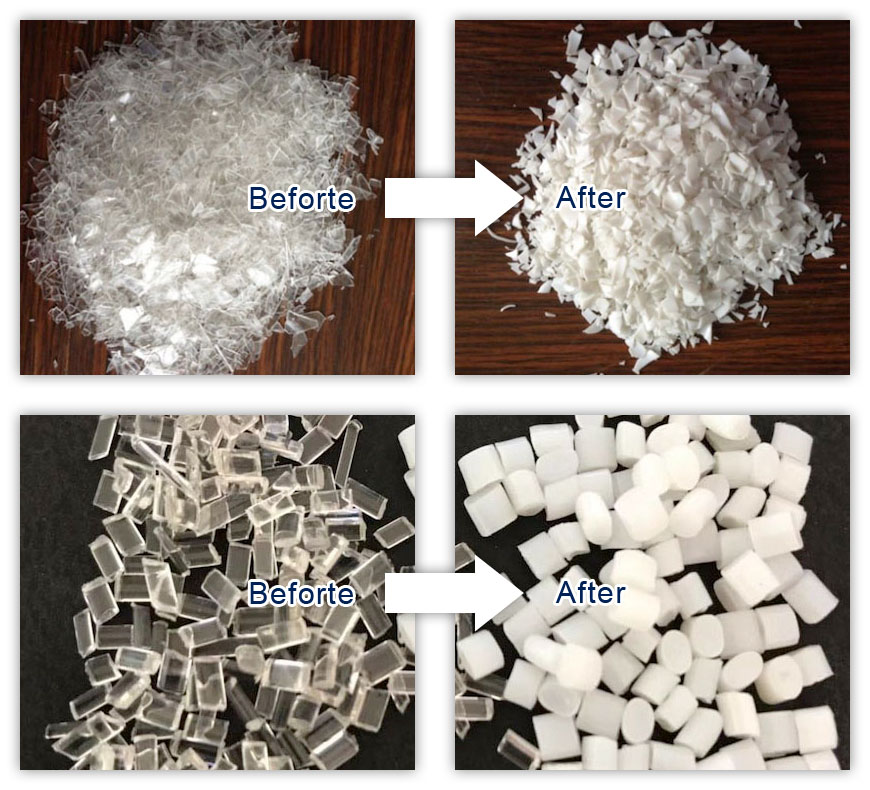
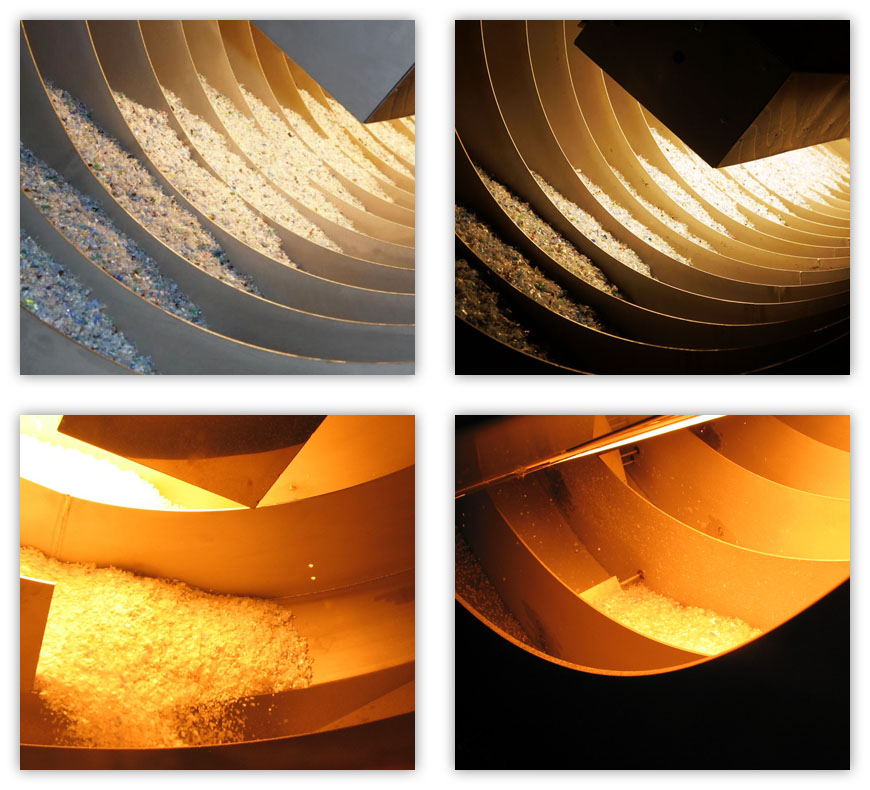